제조 조직 중 이미 디지털 트윈을 사용하고 있는 비율은 몇 퍼센트일까요? 언제 도입했을까요? 어떤 용도로 사용하고 있을까요? 이러한 질문과 그 이상에 대한 답변을 제공합니다.
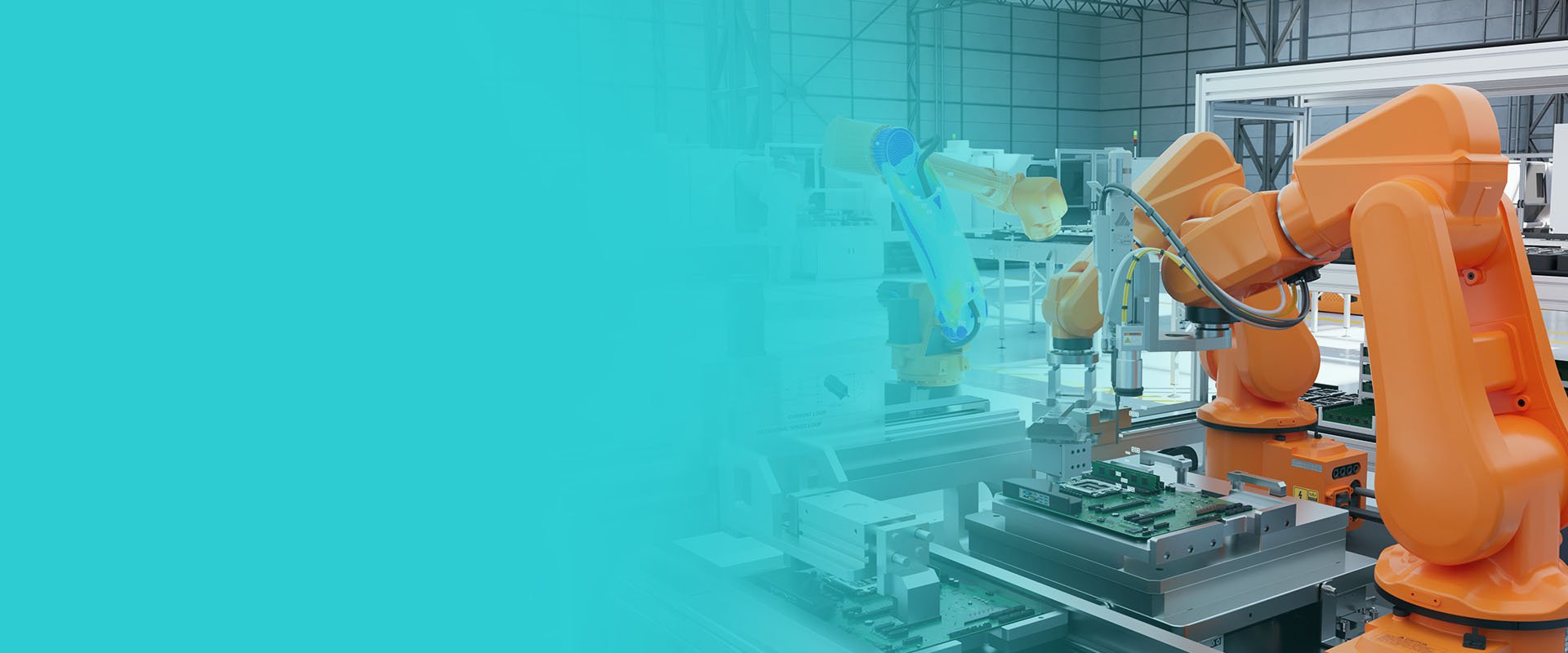
제조업 최고의 디지털 트윈 기술 솔루션
모든 제조 공정의 목표는 고품질 제품을 완벽하게 설계하고 제작하는 것입니다. 업계 최고로 손꼽히는 시뮬레이션, 인공 지능(AI), 데이터 분석, 고성능 컴퓨팅(HPC) 솔루션인 알테어의 포괄적인 디지털 트윈 솔루션을 통해 혁신을 실현하고 시간을 절약하며 낭비를 최소화하는 탁월한 엔드투엔드 성능을 확보할 수 있습니다.
알테어의 디지털 트윈 솔루션은 가상 커미셔닝, 시뮬레이션 기술, 디지털 스레드 통합, 실시간 자산 관리를 통해 제조업체의 역량을 강화합니다. 가상 커미셔닝 및 시뮬레이션 기능을 활용하여 제조 시스템을 구축하기 전에 최적화함으로써 비용을 절감하고 위험을 최소화할 수 있습니다. 또한 제품 라이프사이클 전반에 걸쳐 디지털 스레드를 원활하게 통합하면 실시간 자산 모니터링 및 관리가 가능하므로 유지보수 일정을 최적화하고 장비를 개선할 수 있습니다.
제조 부문에서 알테어의 디지털 트윈 기능은 경량화, 토폴로지 최적화, 멀티피직스 시뮬레이션, 모델 기반 개발 등을 포괄합니다. 전 세계 디지털 트윈에 대한 종합적인 가이드를 찾고 계신가요? 2022 알테어 디지털 트윈 글로벌 설문조사 보고서를 읽어보세요.
제조업 디지털 트윈 인사이트
디지털 트윈 도입이 전 세계 산업계를 휩쓸고 있는 이유와 이 기술이 조직의 워크플로, 제품 및 프로세스를 개선하는 방법에 대해 알아보세요.
알테어의 기술과 전문가가 어떻게 디지털 트윈 여정을 시작할 수 있는지 알아보십시오.
문의하기제조 디지털 트윈 센트럴
디지털 트윈 적용 사례

Digital Twin for Sustainable Energy
Improving lifetime value of a fusion powerplant using a physics-based digital twin. Assystem is an international engineering and digital services group focused on low-carbon projects that accelerate the transition to clean energy. Assystem is committed to the development of decarbonized electricity (fusion energy, renewables and electricity grids) and clean hydrogen. The Assystem team wanted to leverage the expensive design models to create a digital twin by inputting the sensor data that was livestreamed from the plant, which helps engineers understand the plant's structural integrity and further optimize inspection and maintenance schedules.

Digital Twins Boost Barista - Altair® Helps Gruppo Cimbali Speed up Innovation and Go-to Market
As a key to growth in the coffee machine industry, innovation has always been a core pillar of Gruppo Cimbali’s company philosophy. Investing in the research and development of high-performance machines is a strategic decision, and Gruppo Cimbali is proud to be recognized as one of the first companies in the sector to expand into telemetry, Internet of Things (IoT), and Wi-Fi connected machines. To continue to deliver on its innovation promise, the company now applies digital twins – utilizing Altair Activate® – to their development processes enabling it to design better products, shorten development times, and increase energy efficiency.

Digital Twin Implementation: A Strategic Tool to Improve Process/Product Capabilities in Sheet Metal Forming
Sheet Metal Forming has different and wide industrial applications (Automotive, White Goods, Aeronautic, etc....). In the metal forming industry, the simulation of processes and the resulting material behavior is of high importance. Important process parameters (e.g., material flow, temperature range, force required), as well as the resulting material characteristics (e.g., strength, residual stress, temperature resistance), can be supported using FEA to replace costly and uneconomical practical tests.
The re-use of knowledge gained from these FEA simulations in combination with data provided by different sensors is the next step towards the implementation of a Digital Twin. Its integration into the IT architecture of a digital factory is inevitable to increase the efficiency and environmental sustainability of processes and products in manufacturing. Therefore the presented project relies on Reduced Order Models in use of Machine Learning approaches as well as an IoT-based dashboard for the combined visualization of actual data and derived KPIs. As a result, the implemented solution enables significant improvement of capabilities in the considered context.

Digital Twin Platform for Optimized Product Performance | Altair
Digital twins help organizations optimize product performance, gain visibility into the in-service life of a product, know when and where to perform predictive maintenance, and how to extend a product’s remaining useful life (RUL). The Altair digital twin integration platform blends physics- and data-driven twins to support optimization throughout the products lifecycle. We take a complete, open, and flexible approach that enables your digital transformation vision on your terms.